New nickel-plated materials to replace the high-performance aluminum alloys.
Additive manufacturing company Oxford Performance Materials (OPM), based in Connecticut, is a leader in both high performance additive manufacturing (HPAM) and advanced materials science. Back in 2014, the company used its patented OsteoFab technology to manufacture a customized implant for a Somali woman who grew up with a hole in her face from a bullet, and more recently, advanced composites manufacturer Hexcel made a strategic investment in the company, in order to work together to leverage its technology to advance additive manufacturing in aerospace. OPM’s latest news also centers around the aerospace industry: this week, the company announced the commercial launch of its new nickel-plated OXFAB-Ni.
Founded back in 2000, the company has three strategic business units: OPM Biomedical, the first company to receive FDA 510(k) clearance to manufacture 3D printed patient-specific polymeric implants; OPM Materials, which develops the company’s proprietary OXPEKK (poly-ether-ketone-ketone) thermoplastic products; and OPM Aerospace & Industrial. This last business unit produces 3D printed OXFAB production parts for demanding aerospace, defense, and satellite applications.
3D printed parts that will replace the high-performance aluminum alloys currently used in industrial and aerospace applications. OXFAB is designed to be a solution for these highly demanding end-market applications: structures made using the OXFAB selective laser melting process considerably reduce the cost, weight, and time-to-market. These reductions are defined, in the large OPM B-Basis database, in a specific set of performance attributes; the database was developed together with aerospace industry heavyweights Northrop Grumman and NASA.
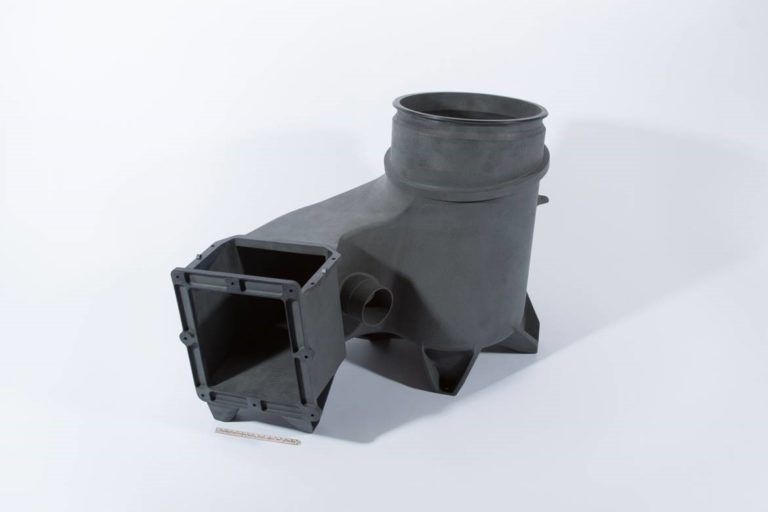
In the aerospace and defense industry, weight reduction and functional complexity really help increase the performance of a part, as well as lowering the overall cost and energy. As mentioned previously, OXFAB manufacturing can help lower the weight of the part: the process combines high-performance thermoplastic and robust additive manufacturing technology, which results in industrial structures that meet, and even go beyond, expectations for many industrial sectors; not just aerospace and aviation, but the energy, nuclear, and semiconductor fields can also benefit.
“We are very pleased to commercially launch OXFAB-Ni as this proprietary technology builds on our existing product portfolio to provide our customers with a new high performance additive manufacturing solution. With the launch of OXFAB–Ni, OPM can now offer our aerospace and industrial customers nickel-plated, fully functional end-use 3D-printed structural parts with a flexural strength-to-weight ratio equivalent to high performance titanium alloys such as 6AL-4V,” said Lawrence Varholak, President of OPM Aerospace & Industrial.
Some of the most beneficial performance characteristics of OXFAB-Ni include:
- Offers near limitless shapes
- Effective shield against radiation
- Allows for rapid manufacturing
- Capable of reaching up to 375°F
- Same strength and weight as high-performance aluminum alloys
The main construction material for OXFAB-Ni is the company’s proprietary OXPEKK formulation. The polymeric material offers high purity and gamma stability, extreme temperature tolerance, very strong mechanical performance, and a very high resistance to chemicals.
This article was written by Sarah Saunders for 3dprint.com
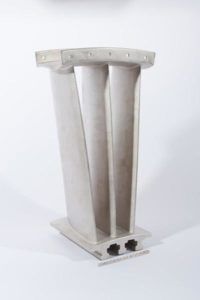
OXFAB–Ni Plated Fan Exit Guide Vane (22” H)
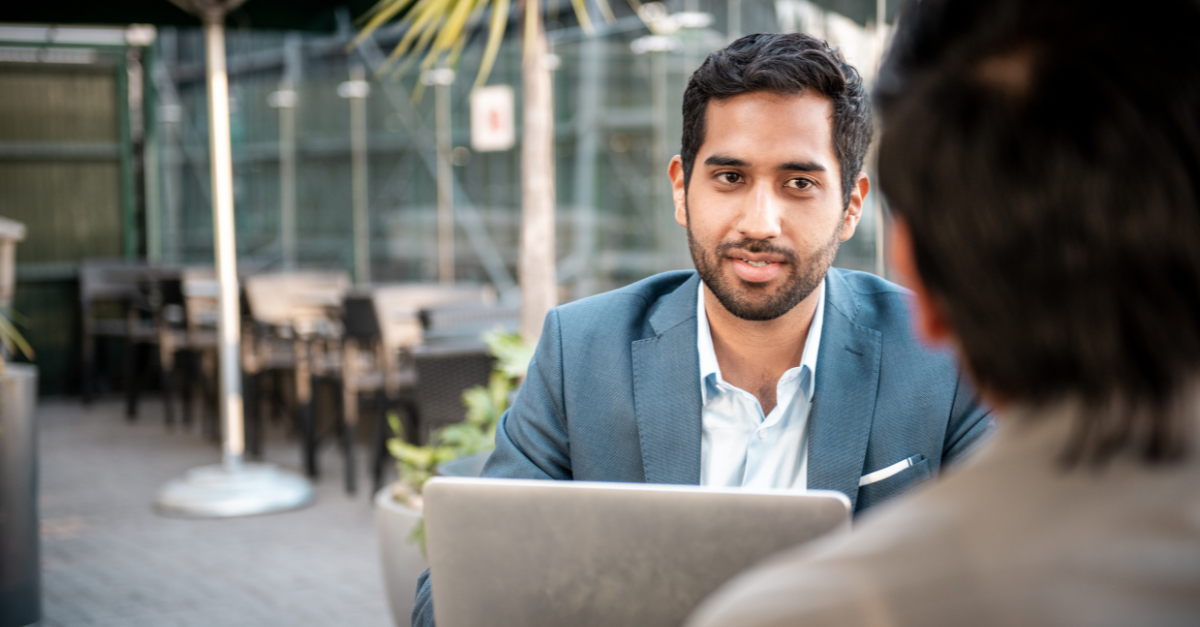
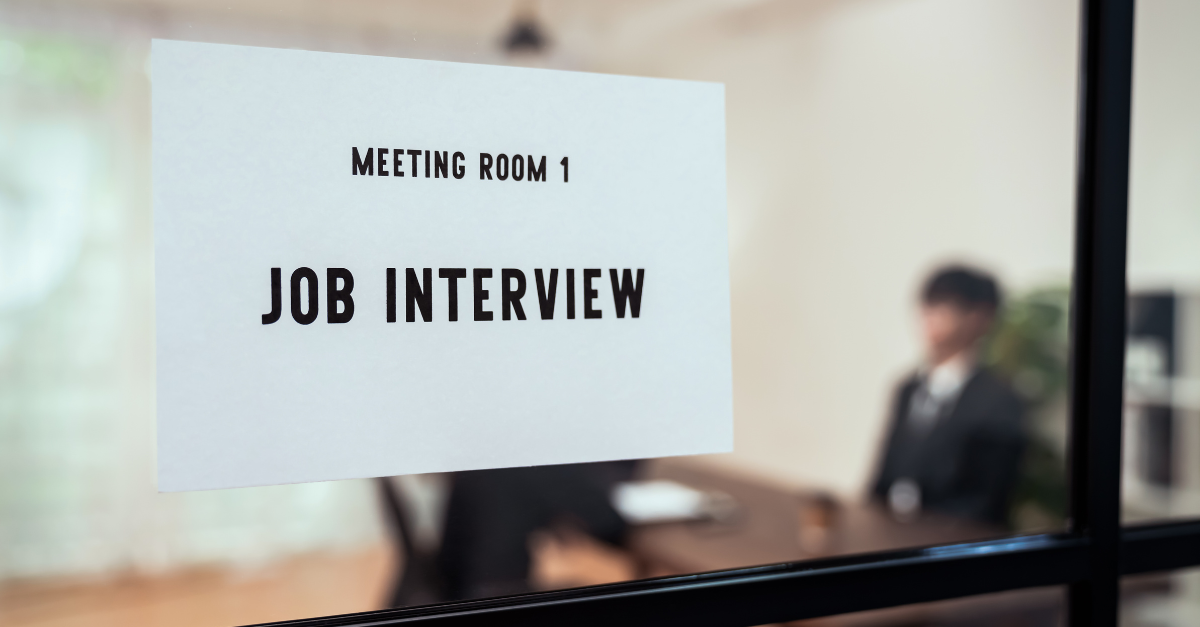
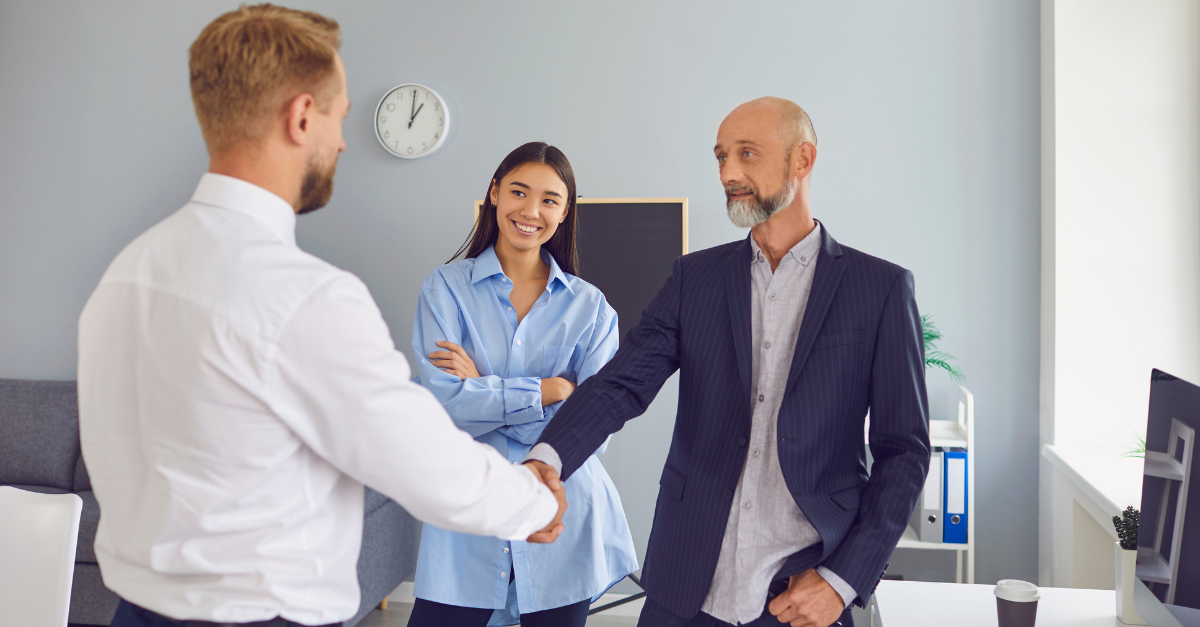
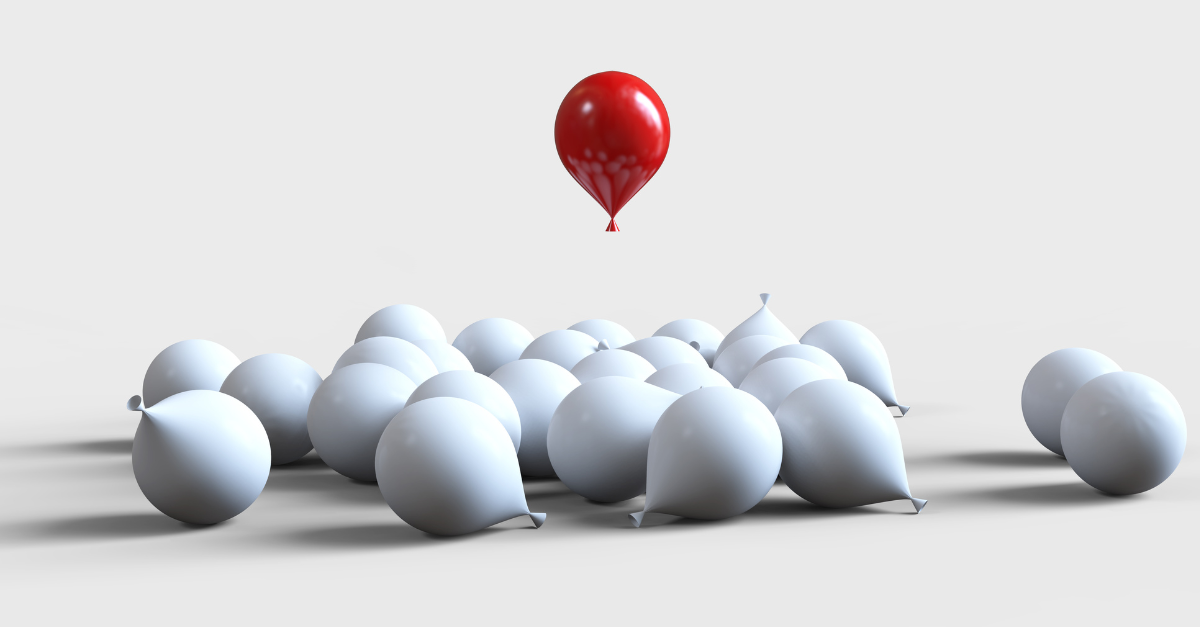
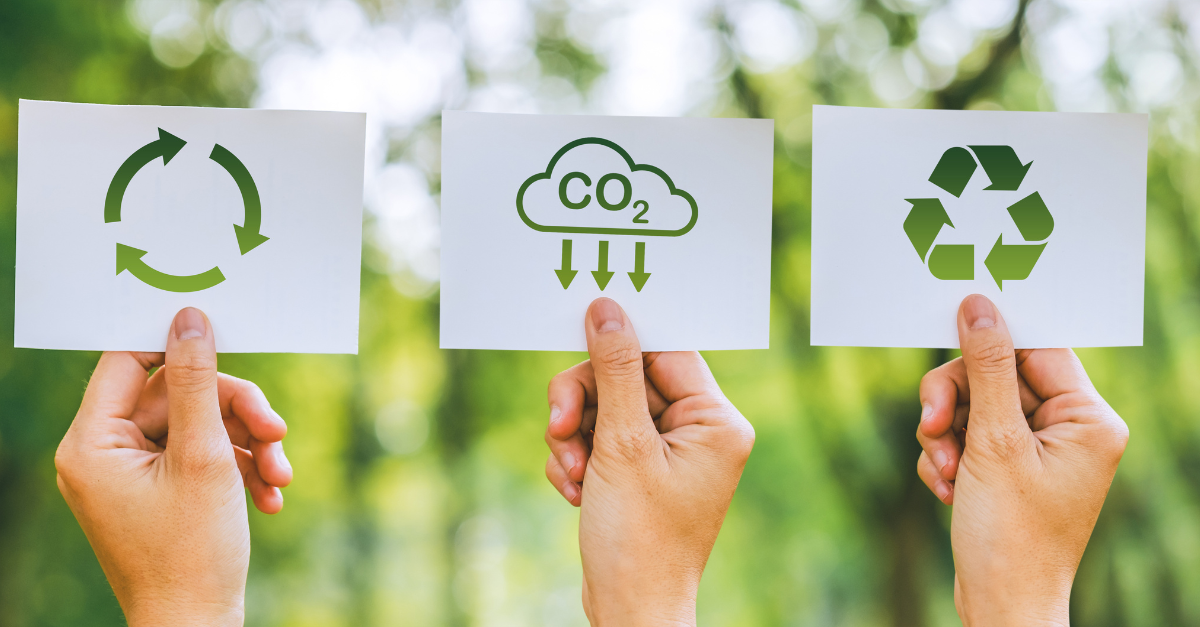
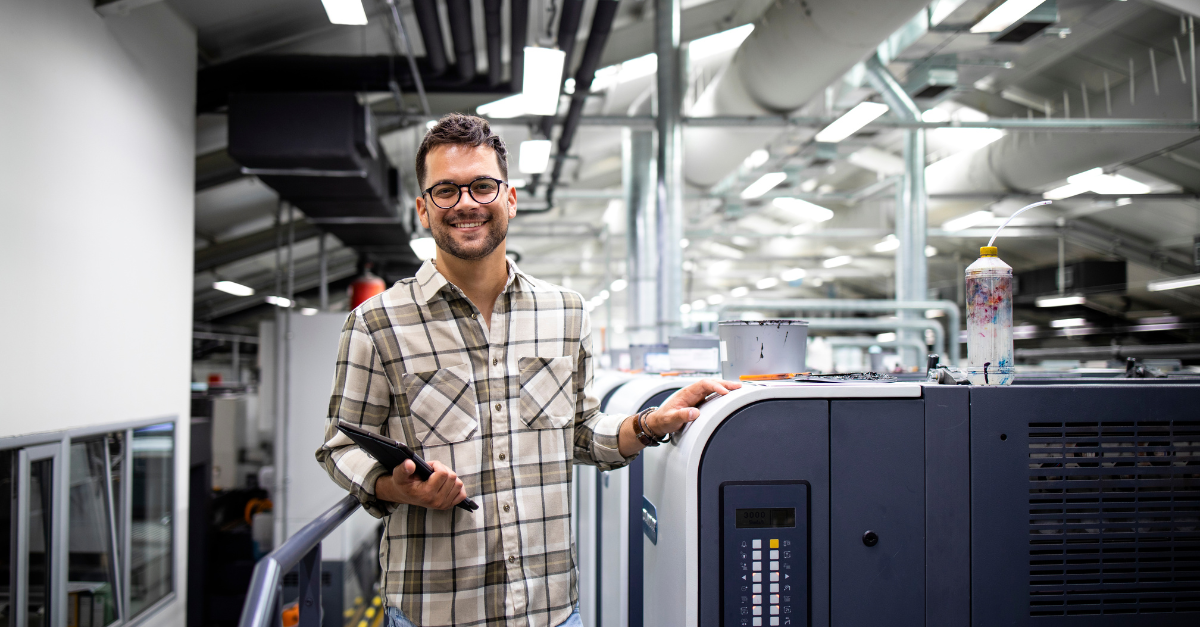
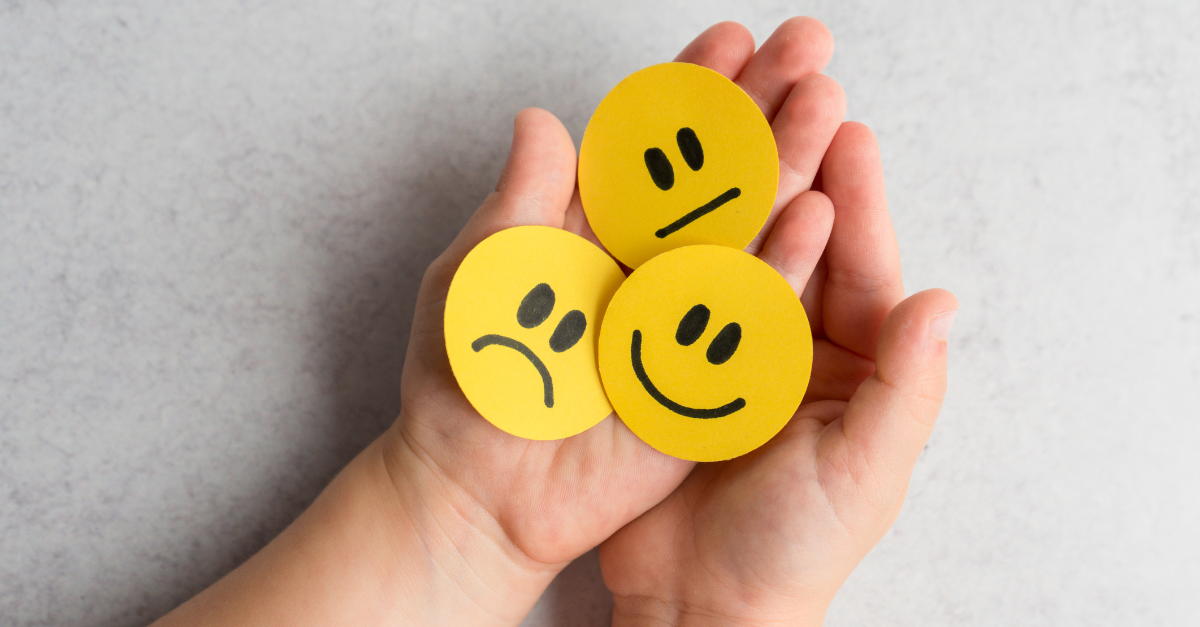
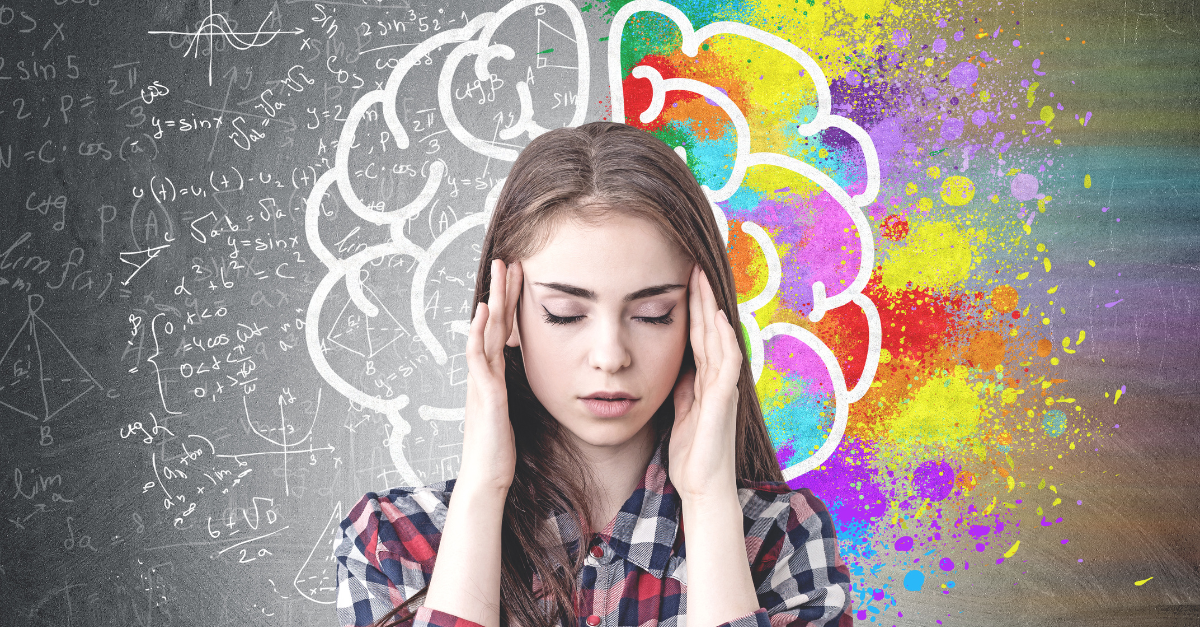
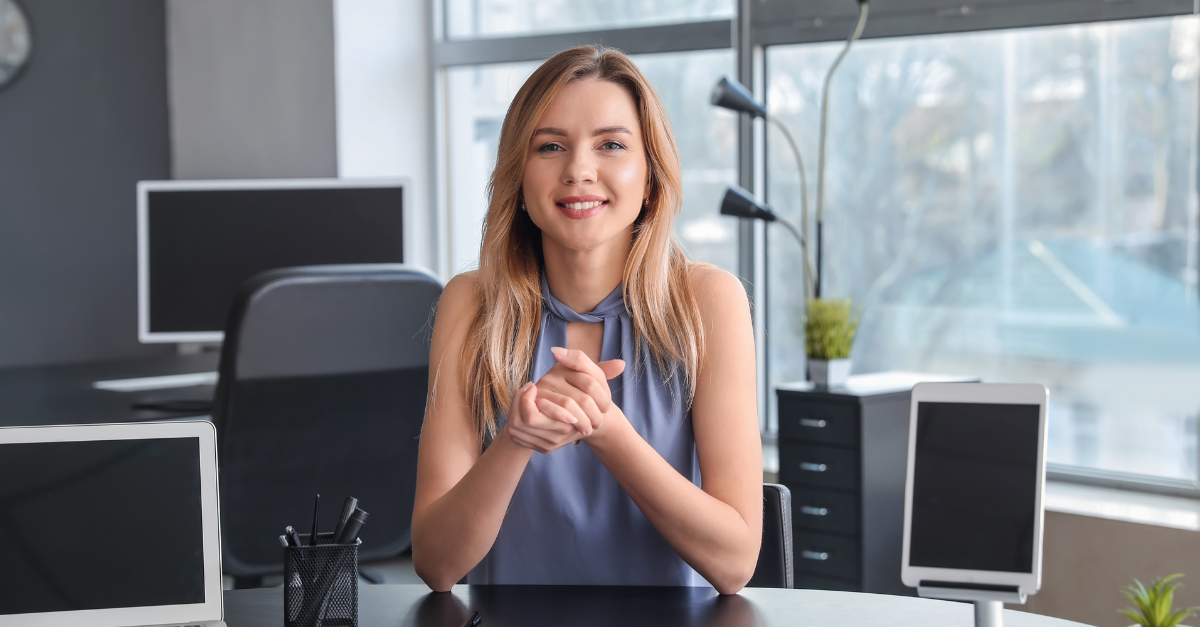
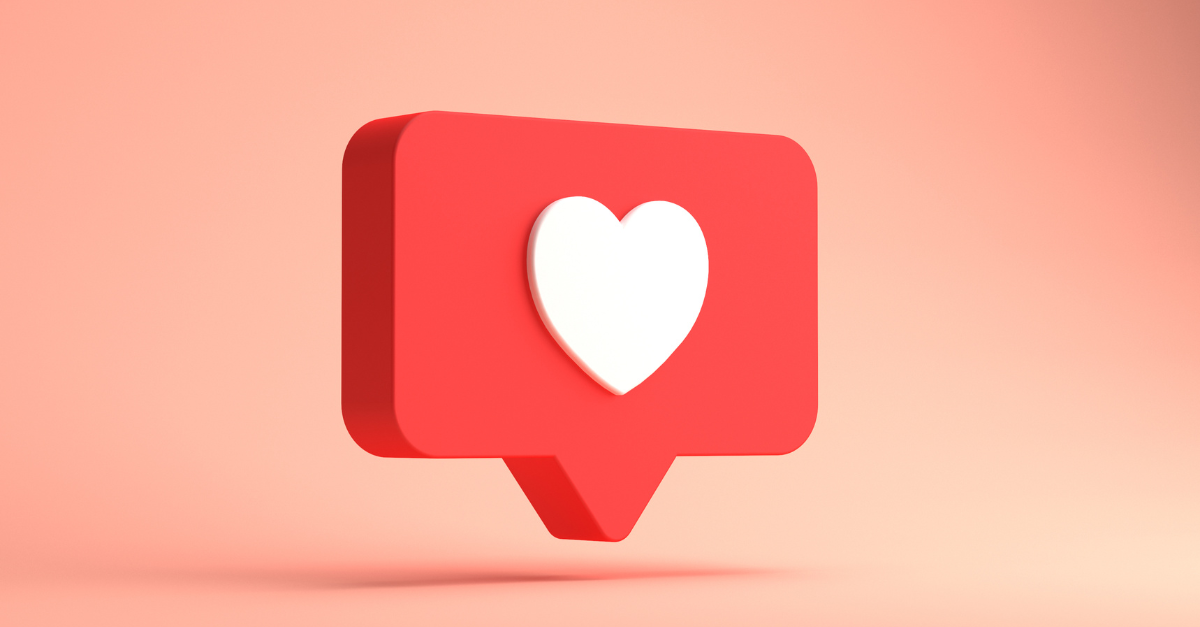